Companies around the globe are looking for new solutions for their challenges:
- How to increase the use of low-carbon fuels.
- How to find technology for using low-carbon fuels.
- How to generate electricity close to the end-user.
- How to complement gaps in renewable generation.
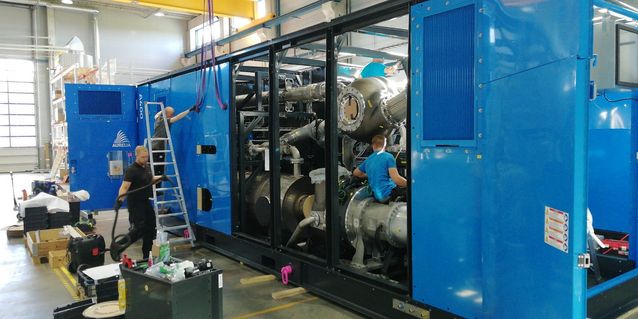
Aurelia Turbines offers its clients several benefits:
- fuel-agnostic on-site energy generation
- cleaner fuel capabilities
- independence and energy security
- greater fuel efficiency, thermal efficiency and lower emissions
Aurelia’s systems, which incorporate a low emission combustion process, can use hydrogen-rich fuels in addition to biogas, synthetic gas as well as other renewable and non-standard fuels. Aurelia's gas turbines provide clients with the flexibility needed to balance changes in renewable energy generation.
The Aurelia® A400 turbine is ideally suited for small-scale combined heat and power (CHP) generation in decentralised grids across the world: it has been designed to meet the needs of small- and medium-sized industrial processes. These 400 kWe turbines may be up to 20% more energy efficient than other microturbines of the same size currently on the market.